Case Study - Kamei Shindo
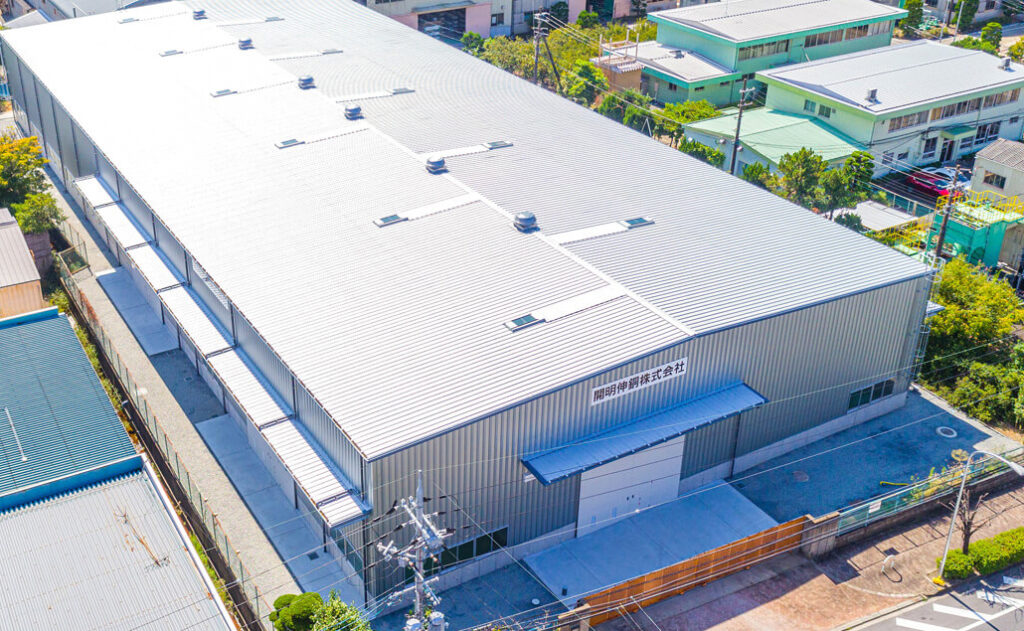
Brief information about the company:
Name: Kamei Shindo
Number of Employees: 119 (As of January 2021)
Location: Kyoto prefecutre, Kameoka city
Founded in 1952 May
Industry:
Copper alloys, alluminium products manufacturing
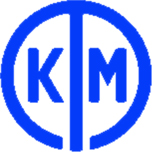
Achieved reduction of phone and FAX tasks by deploying EDIFAS and succeeded in reducing business hours by 20% in less than a month
Kaimei Shindo Co., Ltd. is a copper alloy and aluminum manufacturer established 69 years ago in Kyoto. Since its founding, they’ve found a high-mix, low-volume production system and built up a history of more than 60 years based on its advanced technological capabilities. Especially in the copper alloys area, they specialize in the unique shape of brass and have a domestic market share of more than 80%. Kamei Shindo offers its customer’s an integrated production line from mold making to extrusion and processing. We asked Mr. Tadayuki Okumura, Corporate Planning Office, Administration Headquarters, about the background of deployment of the cloud-based EDI service “EXtelligence EDIFAS” (from now on referred to as EDIFAS) and the tasks that were solved by deploying and using EDIFAS.
-Could you tell us why you decided to deploy EDIFAS?
The reason for deploying EDIFAS was that we felt a problem in the data entry tasks. Before the deployment of EDIFAS, communication with customers was done via phone and FAX. Therefore, it was necessary to enter the information received from customers into the system manually, which took a lot of time and effort. When taking advantage of the version upgrade of the core system “Factory-ONE,” we learned that the time and labor required for manual data entry could be significantly reduced by linking the systems, so we decided to deploy EDIFAS. Because it was possible to integrate these two systems seamlessly, we even didn’t consider other options.
-What did you manage to achieve by deploying EDIFAS?
With the deployment of EDIFAS, we considerably reduced the amount of paper used, man-hours for manual data entry, and careless mistakes such as data entry and calculation errors. We continue to use telephones and FAX for half of the operations. Still, for the other half, we use EDIFAS, which led to a maximum reduction of about 20% of business operations per day. In the conventional method, manual entry was the majority, so entry and calculation errors inevitably occurred. Still, since it became possible to exchange data after the deployment of EDIFAS, we no longer worry about such errors, as they are eliminated to the maximum level. In addition, the accuracy of business operations management has been dramatically improved, and not only productivity and efficiency have been improved throughout the business, but also smooth communication with business partners has been enabled.
-Did you feel any troubles or difficulties during the period from implementation to operation?
At the beginning of the deployment, we felt that it would take some time to get used to EDIFAS because of organizing what we were entering manually and what we were handwriting and changing the operation type. However, since EDIFAS interface is user-friendly and very easy to operate, we got the hang of it without any problems in less than a month. Now, it is possible to work with less than half the labor we had before, and some members from the field are asking: “Why don’t other business partners use EDIFAS?”
-Could you tell us about your future plans?
We, Kameishindo, will keep leveraging all the potential of EDIFAS and Factory-ONE from now on. It’s convenient that we don’t need to ask multiple companies to deal with integration between Factory-ONE and EDIFAS, as EX does all the required work. In addition, they respond to and solve any urgent issues remotely, which enables smoother operation.